Otimização de Layout - história e importância para a produção
- elementusjr
- 7 de fev. de 2020
- 2 min de leitura

No ano de 1913, Henry Ford instalou a primeira linha de montagem para possibilitar a produção em massa de automóveis. O tempo de montagem do Ford Modelo T produzido nessa linha passou de 12h para 2h30min. O projeto foi baseado no funcionamento de algumas fábricas de Chicago da época.
Anos depois, baseado no modelo de Ford, surgiu o Sistema Toyota de Produção. Esse novo sistema melhorava a qualidade dos produtos e ainda eliminava grande parte dos desperdícios (um dos principais defeitos do modelo Ford).
Os impressionantes resultados obtidos por ambos os modelos tiveram, em sua essência, a preocupação enorme com o layout da fábrica para que o fluxo produtivo ocorra de forma mais eficaz e eficiente, aumentando a produção e reduzindo o tempo dos processos. Desse modo, a disposição de máquinas, recursos, equipamentos e o posicionamento de armazéns e estoques de materiais devem possibilitar o acesso rápido, pouca necessidade de movimentação e fácil identificação.
Algumas das situações que geram a necessidade de melhores configurações de um layout industrial são:
Alterações no projeto dos produtos, que demande o uso de novas máquinas ou processos;
Necessidades de expansão da área produtiva em função de aumento de demanda ou introdução de novas matérias-primas;
Necessidades de crescimento de algumas áreas específicas ou departamentos da organização;
Criação de novas áreas ou departamentos, realocações de unidades;
Instalação de novas plantas industriais para expansão de capacidade ou introdução de novas linhas de produtos.
Independente da da origem do problema, a otimização do layout sempre está ligada às questões abaixo:
1)Dimensões, peso, volume ocupado pelos produtos: quanto mais pesados e difíceis de movimentar, maior a necessidade de equipamentos de auxílio a tarefas de elevação e transporte (pontes rolantes, guinchos, elevadores), e maiores as necessidades de mão de obra e de tempo. Assim, nestes casos, deve-se configurar o layout de modo a evitar movimentações dos produtos.
2)Complexidade dos produtos: quanto maior o número de componentes, maior a necessidade de operadores para movimentar o material entre os postos de trabalho.
3)Relação entre os tempos de operação e de movimentação: quanto maior a proporção dos tempos de movimentação de materiais e componentes, em relação ao tempo de processamento (operações de transformação), maior importância deve ser dada para as configurações que reduzam as necessidades de movimentos, para aumentar a produtividade.
Veja abaixo as principais etapas para determinação do layout industrial:
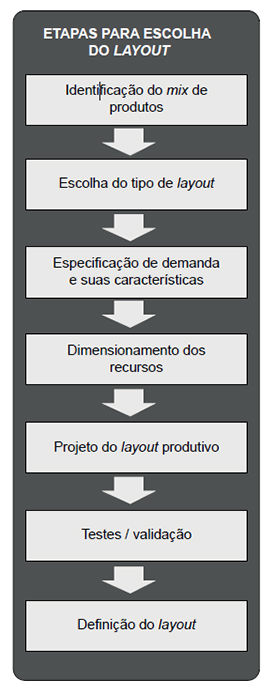
Para que a otimização do processo retorne o melhor resultado possível, as informações necessárias em cada etapa devem ser determinadas ou conhecidas pelo responsável do setor com a maior precisão possível.
Erros nos dados ou previsões equivocadas podem causar falhas na tomada de decisão que comprometerão todo o projeto.
Outro aspecto importante diz respeito à composição dos produtos: a identificação de cada insumo deve ser acompanhada de informações completas sobre os produtos, principalmente relativas ao ciclo de vida de cada um. Esta informação é fundamental, pois permitirá considerar efeitos de médio e longo prazo relativos a sazonalidade (ciclicidade) e tendência na especificação das demandas.
Se você se interessou e necessita de ajuda para otimizar processos da sua fábrica, solicite um "Projeto de Layout" contatando a Elementus Júnior Consultoria pelo número (81) 3103-9033 ou preenchendo o formulário em nosso SITE. Entraremos em contato com você para esclarecer quaisquer dúvidas!
Fonte: Manufatura em foco
Comments